How our Diamond Disks are Different
Many companies out in the world make diamond disks, so why should you choose our disks over any other manufacturer?
We're glass workers with over 30 years of coldworking experience. We know what a tool needs to work well on the glass. We don't purchase our electroplated and resin diamond disks from other companies; we manufacture them ourselves in our facility in North Carolina.
We don't just mass-produce disks, but we take the time to ensure our electroplated disks have the right combination of the correct forms of natural diamond to make a disk that cuts quickly and lasts for a long time with consistent cutting results.
We maintain our plating tanks and keep our chemistry in the right parameters to maintain a consistent, high-quality plating layer so your disk is the highest quality we can manufacture.
If you have a problem with your disk, we stand behind our product and will replace it if it has any fault from the plating process.
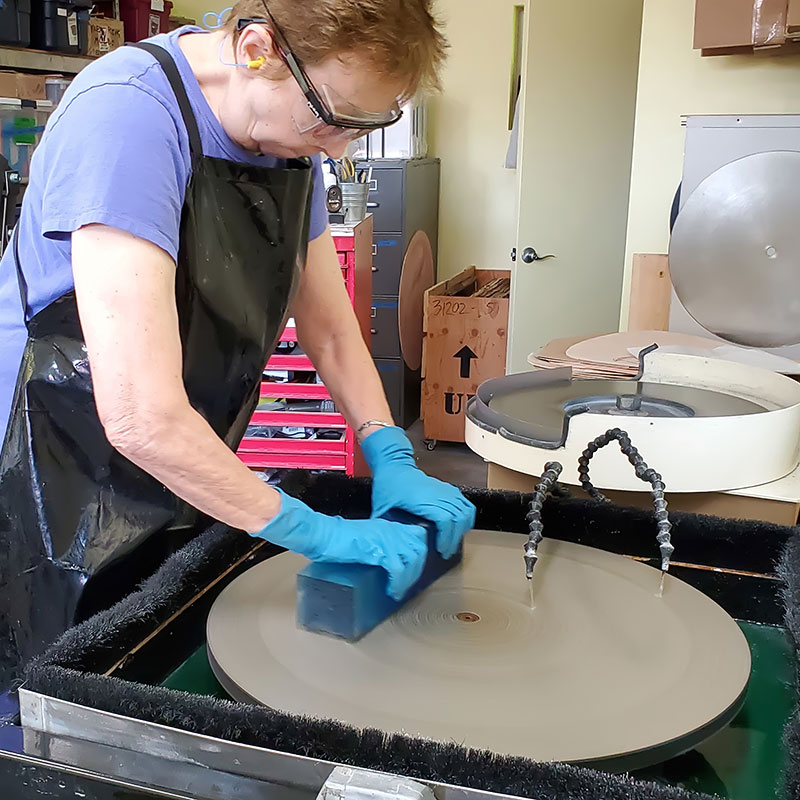
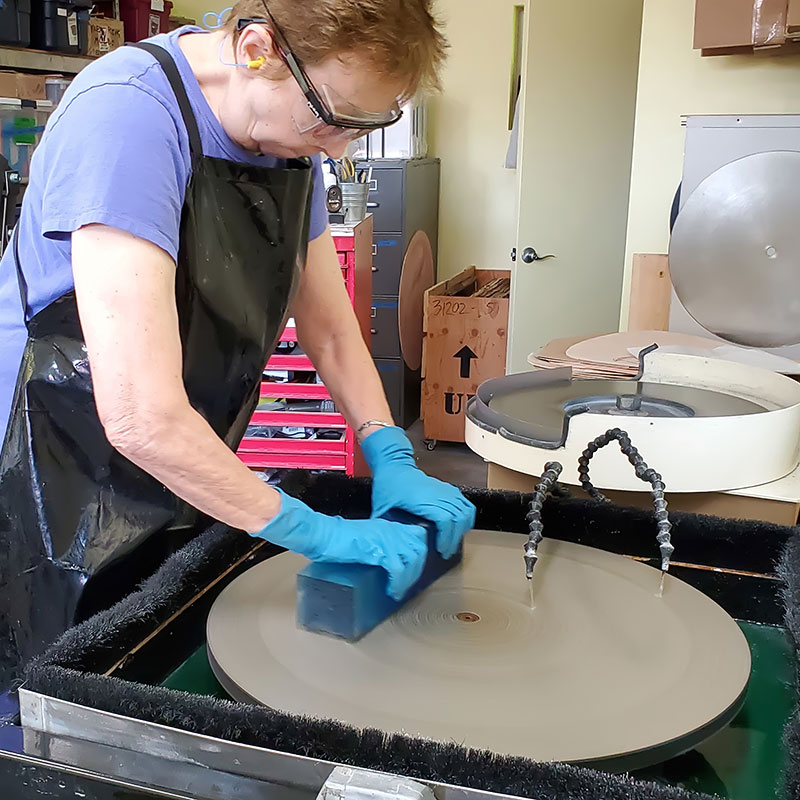
Natural Versus Synthetic
You've probably seen electroplated diamond disks that appear "loaded" with diamonds. They're almost bunched on top of one another on the disk's surface. These disks will also have a "yellow" appearance on the surface of the diamond.
These are synthetic, lab-grown diamonds. While they are inexpensive, they are also less long-lasting than natural diamonds. They break more quickly and leave a dull edge when they break. The disks are loaded with diamonds because they will fail more quickly than natural diamonds.
The problem with a surface loaded with diamonds is it will behave like a tabletop and support the glass more than grind it. You need space between the diamonds for them to work effectively as a grinding medium.
ÂOur electroplated diamond disks use all-natural diamonds for the longest-lasting, highest-cut-rate disk surface we can make.
We utilize synthetic diamonds on our rougher grit disks, like the 30, 45, and 60-grit disks, as fillers to maintain the correct spacing of diamonds, but they are not meant to be used as a grinding agent on the disk surface.
How are Resin Diamond Pads Different from Electroplated?
That's a great question!
While our electroplated pads have a fiberboard substrate, the resin diamond pads have an optical felt substrate.
Instead of locking the diamonds on the disk's surface with nickel, the resin-based diamond pads mix the diamonds into a resin applied to the optical felt substrate. When cured, this layer of diamond material stays flexible on the disk's surface.
The upside is that the surface from the resin-based diamond is significantly finer at the same grit level as the surface from an electroplated diamond disk.
This allows the resin pad to create a finer pre-polish finish on the glass, making it easy to transition to a cerium polish.
Login and Registration Form